What is a conductive slip ring
What is a conductive slip ring? Slip rings are electrical components responsible for connecting rotating bodies and transmitting energy and signals. According to the transmission medium, slip rings are divided into conductive slip rings, fluid slip rings, and smooth rings. They can also be collectively referred to as “rotational connection” or “rotational connection”. Slip rings are usually installed at the rotation center of the equipment, and are mainly composed of two parts: rotating and stationary. The rotating part connects the rotating structure of the equipment and rotates with it, which is called the “rotor”, and the stationary part connects the energy of the fixed structure of the equipment, which is called the “stator”. The slip ring as a whole relies on the elastic lap principle, rolling lap principle, or sealing principle, as well as the ingenious motion structure and sealing structure design, precise parts production and coordination, and reasonable material selection, etc., to form a stable and reliable rotation connection system. As long as the slip ring is attached to the infinitely rotating equipment, it can provide power energy to the rotating body, so that the rotating body can perform other movements or detect the working conditions in the rotating state while rotating infinitely.
Conductive slip rings are the most widely used in all slip ring series. They are also called brushes, carbon brushes, collector rings, collector rings, collector rings, swivels, and rotary electrical joints. They are specially used to transmit power supply and signal power supply during unlimited continuous rotation. The stator and rotor parts respectively lead out wires to connect the power supply and terminal electrical appliances of the fixed structure and the rotating structure, and rotate with them.
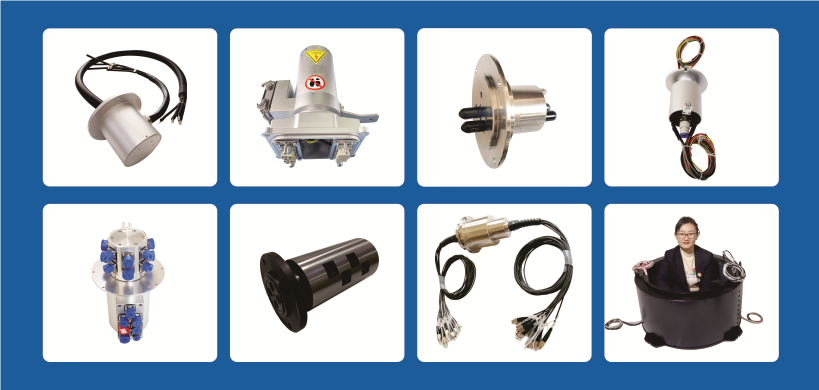
1.According to their overall structure and design, conductive slip rings can be divided into the following categories:
Hollow shaft slip rings, cap slip rings, split slip rings, disc slip rings, optical fiber slip rings, wind power slip rings, high-speed and high-frequency slip rings, etc.
2.The application of conductive slip rings is extremely wide, and the specific industries can be divided into:
Security, medical equipment, aerospace, shipping facilities, radar antennas, wind power generation, robots, video surveillance, engineering machinery, manufacturing and processing control systems, etc.

3.Main features and advantages of conductive slip rings:
- Easy installation, small size, light weight, compact appearance
- Integrated transmission of various complex signals (high frequency/optical fiber/video/high-speed data)
- High stability of slip rings & ultra-long working life
- Gold-gold contacts, extremely low contact resistance
- Easy plug-in design-Harting connector
- Special customization and design can be made according to different needs of users
4.Specific parameters to be provided when selecting conductive slip rings:
- Number of channels
- Working speed
- Working temperature and humidity
- Power circuit (maximum current and voltage must be provided)
- Signal type
- Protection level (some users have harsh operating environments and have special needs in this regard)
5.Common sense in selecting slip rings:
- Brand misunderstanding: Many times, everyone thinks that domestic products are impractical or even unusable; Ingiant Technology’s successful research and development and strict control of product quality have gradually faded this brand misunderstanding. Ingiant has become a domestic first-line brand, which has also been recognized by international peer companies.
- Accuracy misunderstanding: When choosing a product, people always think that accuracy is the most important; in fact, from a certain perspective: stability is more important than product accuracy, and accuracy selection should be based on high stability.
- Pursuit of cheapness: Good quality and low price are what everyone wants to pursue; but in fact, high-quality products are destined to determine that its price will be relatively high. There are many factors involved, such as: high raw material cost, machining costs, mold opening costs, material and manpower requirements.
- Choose the right range, right accuracy, right installation method, and right output method.
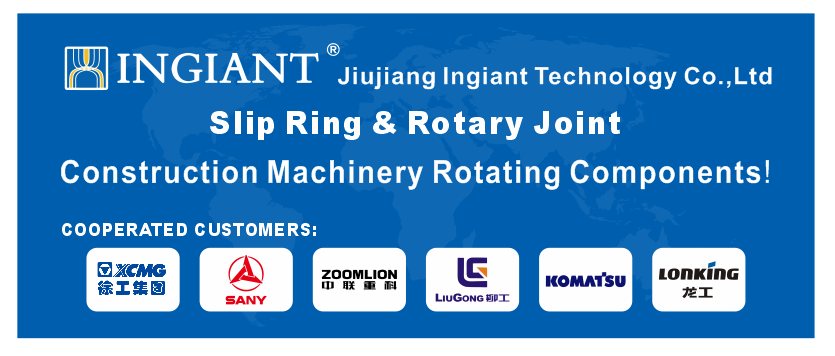